How Suppliers Can Ensure Quality Labels with Automated Barcode Inspection
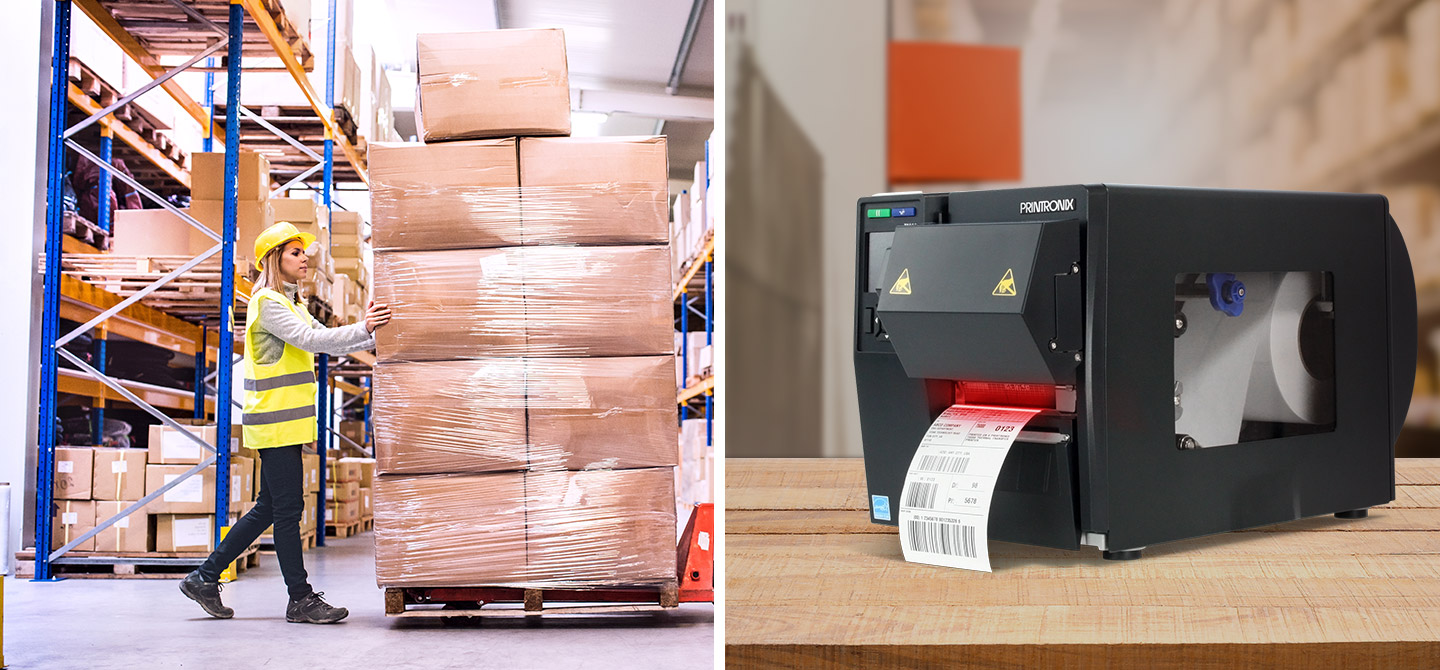
Walmart’s Success and Scale
In his 2005 book, The World is Flat, Thomas L. Friedman noted, “Thanks to the efficiency of its supply chain alone, Walmart’s [sic] cost of goods is estimated to be 5 to 10 percent less than that of most of its competitors.” Innovations such as mandating RFID, relentless automation, and operational improvements have enabled Walmart to continue to grow, “moving 2.3 billion general merchandise cartons a year down its supply chain into its stores.”
Walmart Needs Cooperation and Compliance
The label of an incoming pallet can negate Walmart’s best-laid plans for warehouse efficiency. If the label contains incorrect or incomplete information, or if the label cannot be read instantly to extract the necessary information to tell the forklift driver what the pallet is and where it needs to be, the pallet doesn’t move. This stalls other incoming pallets. In a company that moves 2.3 billion cartons per year (or 73 per second), backups at the receiving dock impact productivity, inventory on store shelves, and, ultimately, the price of products on the shelves.
To discourage suppliers from applying labels that will delay processing at the receiving dock and radically impact productivity, Walmart, like many retailers, has- imposed fines or chargebacks for labels that do not meet specifications. These specifications include a barcode “grade” established by the International Standards Organization (ISO) for providing an objective measurement of barcode readability. There are over a dozen parameters that are individually evaluated and then summarized in a numeric and letter grade similar to the US school system of “A” to “F”. Labels that do not meet Walmart’s grade standards are subject to a chargeback.
For context, in Friedman’s book, he states, “Just one company, Hewlett Packard, will sell four hundred thousand computers through the four thousand Walmart [sic] stores worldwide in one day during the Christmas season.” If even 1 percent of these labels fail to meet the barcode grade and incur a $100 chargeback fee per label, HP could face tens or hundreds of thousands of dollars in chargebacks, consistently.
Automated Barcode Inspection as a Solution for Suppliers
Paying chargebacks is dull not only as it impacts the supplier’s bottom line, but it is entirely preventable. Simply printing a label with a TSC Printronix Auto ID printer with ODV-2D barcode label inspection will automatically read and grade every barcode on every label without any additional hardware, servers, templates, software, or operator intervention. Finding and fixing any barcode issues before the label is applied to a carton or pallet is the most effective and efficient way to reduce chargeback exposure.
An integrated solution, including both ODV-2D barcode validation and a printer, lists for under $3,500. After recouping the initial cost and investment, the savings flow directly to the bottom line. Depending on your enterprise, it could take as little as a few months. These savings is particularly attractive as our products are built reliably durable for many years of use. Not only does this improve the supplier’s margins, but it means that incoming goods will flow more smoothly through the Walmart distribution system helping Walmart keep prices lower.
Walmart is not unique in imposing chargebacks for incoming barcodes that fail to meet specifications. Many retailers and manufacturers face the same issue with productivity if incoming pallets or cartons have poor-grade barcodes. Suppliers can improve their brand reputation with their customers, help ensure smooth supply chain operation, and improve their profitability by inspecting their labels prior to being sent.
If your enterprise is subject to Walmart’s RFID mandate and is required to apply RFID labels to incoming shipments, it does not mean that you have to give up barcode inspection. Our robust, award-winning T6000e industrial printer offers both RFID and automated label inspection in a single machine. RFID labels are automatically encoded and checked, and barcodes are automatically graded all in a single pass through the machine. The backup, overstrike, and reprint capabilities apply to both RFID and barcode labels, ensuring that accurate barcode information reaches your customer’s receiving dock.
To explore how ODV-2D barcode verification and validation can ensure quality labels, contact your local TSC Printronix Auto ID sales representative, or check out our website here.