Barcode Verification Ensures an Efficient Supply Chain
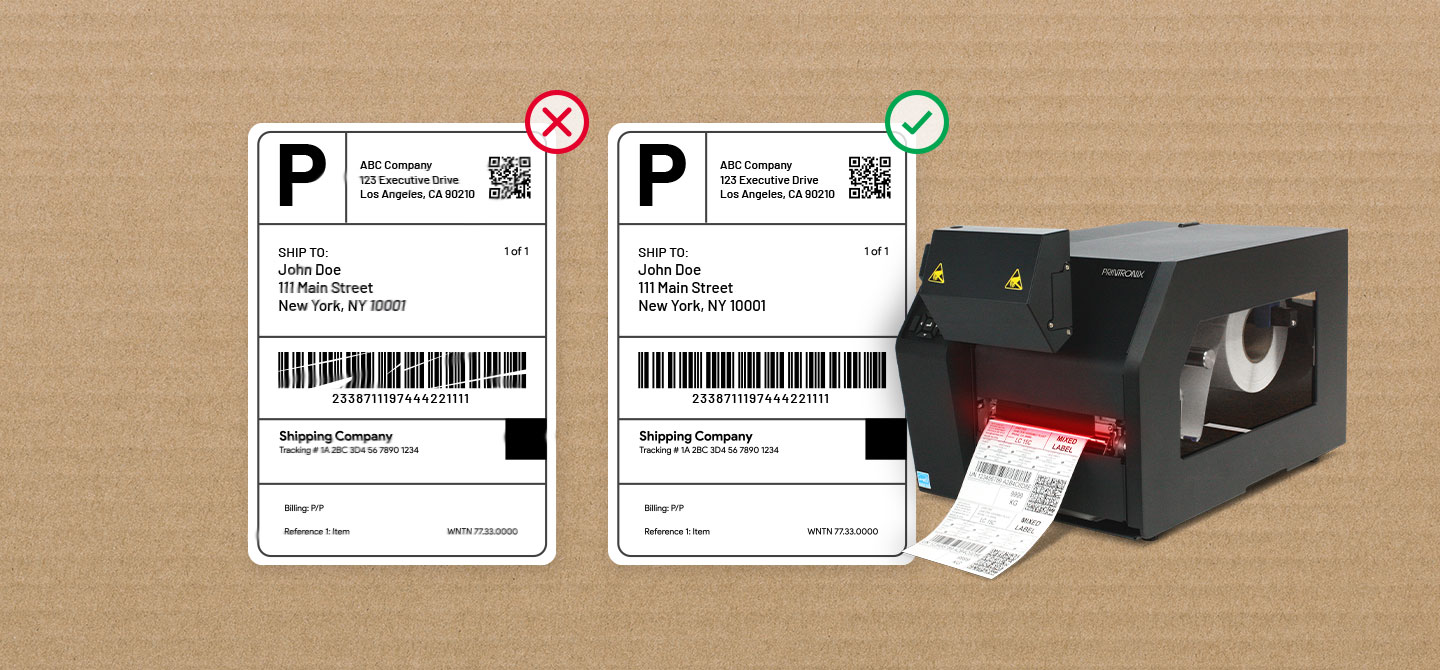
The entire world is struggling with the ripple effects of broken links and backlogs in the supply chain system. Whether the issue is software, truck drivers, port unloading cranes, or processor chips, the single common element is that these goods are being moved around on more than 7 billion pallets in global use.
Pallet labels might not be the most exciting topic on the planet, but they are a critical one. Without a label, a pallet is merely a stack of wood with some boxes on top, going nowhere. The label enables the pallet to move seamlessly through the supply chain network being flown, trucked, carried by sea, and arriving at its destination, routing items to their destination. If a label is missing or unreadable, it can wreak havoc on this process. Today’s blog will show you how integrated ODV-2D can help you prevent bad labels.
Automated Label Inspection Reduces Errors
What appears to be a simple label is actually a powerful tool that conveys directives, enabling the pallet to be routed from its originating location to its destination, globally and domestically. A vast amount of information is conveyed in that small barcode label with the remarkable ability to transfer data almost instantly to the receiver.
Effective barcodes provide the receiver with necessary details such as lot number, manufacturing location, and order number. This provides instant instructions on how to handle the pallet upon arrival.
This efficiency only occurs if the barcode transfers the information successfully. A small glitch at the shipper’s location with the printhead or a ribbon wrinkle could destroy the barcode’s ability to transfer information. A bad barcode could go undetected until the pallet arrives at its destination and the receiving location cannot extract the data needed to process the pallet.
Spot checking labels using a manual inspection process requires additional operator intervention and, by the definition of spot checking, doesn’t check all the labels. Manual checking also requires additional space and equipment investment in servers, software, templates, and monitors.
Our robust ODV-2D barcode label verification and validation printers are equipped with a fully automated, built-in barcode verifier that grades and validates barcodes to ISO standards. This is more efficient than other inspection solutions because it automatically identifies bad labels during the printing process and overstrikes and reprints them without requiring operator intervention.
Ensure Quality with the T6000e and T8000 ODV-2D Printers
Avoid delays in transportation, returned goods, or even fines and chargebacks from the receiving location by inspecting the pallet label before it’s applied. By far, the easiest way to do that is with an integrated barcode verification scanner inside the printer. This enables you to simply print the label and eliminates software, controllers, and operator intervention.
The T6000e and T8000 enterprise-grade printers have an ODV-2D barcode inspection option which automatically locates and grades every barcode on every label for every job—to ISO standards—by simply printing the label. The ODV-2D barcode inspection printer and scanner talk to each other, enabling the scanner to know the location of every barcode label printed. If a bad barcode is discovered, the scanner tells the printer to back the bad label up and overstrike it, so it is not used, automatically reprinting the label.
This process ensures your pallet labels are accurate and routes goods to the proper destination.
Efficient ODV-2D Barcode Inspection, Great ROI
As the leaders in ODV-2D barcode inspection integrated label verification, we offer one of the most efficient ODV-2D label inspection systems on the market. By improving efficiency, reducing errors, and often reducing chargebacks, our printers provide outstanding value and a great ROI.
Contact your local TSC Printronix Auto ID representative to get started with integrated ODV-2D barcode inspection and validation today.