How to Auto-Detect and Fix Failed Labels While Printing to Save Time, Money, and Your Brand Reputation
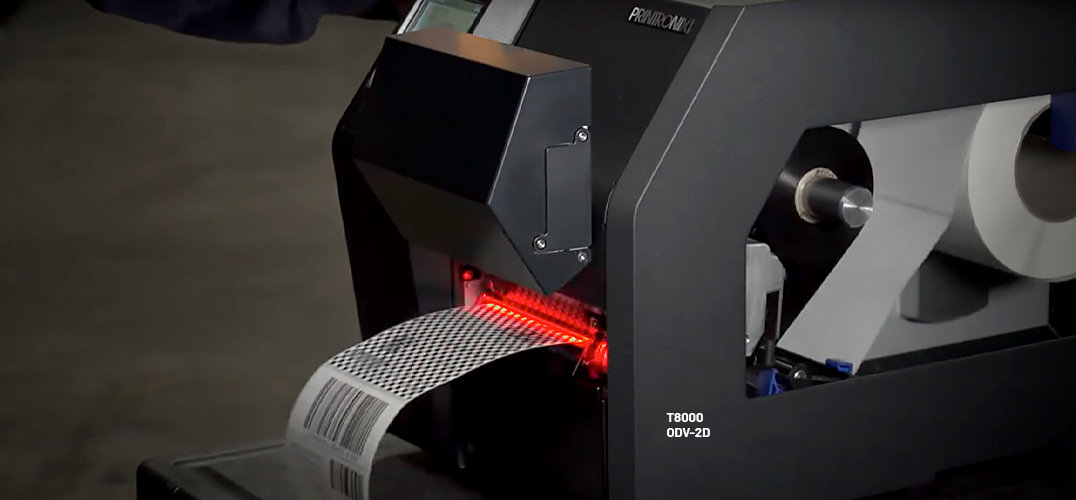
There is a saying in development and manufacturing that often holds true. The longer you wait to solve a problem, the more expensive it becomes to fix it. Apply that to shipping labels. When do you want to identify a non-compliant barcode label: Before it leaves your facility or when it arrives to its destination, risking costly fines and other penalties?
Read our latest blog that highlights the challenges of fixing unreadable labels with end of line scanners and offers a solution to help you save time, money, and your brand reputation by enabling automated label correction during the printing process.
Non-Compliant Labels Slow Productivity, Drive Penalties
Retailers and manufacturers have little tolerance for incorrect or unreadable labels. This is because major retailers and distributors operate high volume production environments that receive and process up to hundreds of pallets every hour. If an incoming shipment container label is unreadable, productivity is slowed, costing time and money. The receiver of a shipment with a bad barcode label may respond to the non-compliant label by issuing fines, chargebacks, rejecting the shipment, or performing forced quality audits.
End of Line Scanner Solutions Lack Printer Integration, Lead to Added Expenses
Companies that generate labels often use an end of line scanner to verify barcode label quality before a package leaves the facility to solve this problem. While this is a good best practice, each scanning station must have a controller for the scanner, software, a template to compare the label against, and a recirculation station within the conveyor system to separate the carton with the failed label out of the process flow. Then it returns to the print station where the carton is manually handled for a label reprint.
While the package has not yet left the building, waiting this long to catch the problem incurs unnecessary expenses. End-of-line equipment used to catch errors is better than not catching a label issue at all. But it requires a setup that is unnecessary for thermal printers. There is a better way to do this with thermal printers that offers a lower cost and simpler solution.
Save Time and Money: Integrated Barcode Inspection within the Printer Footprint
There is an alternative to end of line scanning that saves labor, time, and money. You can detect a failing label while it prints. A Printronix Auto ID printer with two-dimensional online data verification or shortened to ODV-2D is a solution that integrates a scanner within the printer to deliver functional and effective barcode label inspection during the printing process. There is no external PC, monitor, scanner, software, or templates required to deploy the solution. Our printers enhance the process by checking the label while it is still in the printer where you can do something about it. And it doesn’t require additional equipment or space to fix it. The process is identical to printing the label. That’s it. Everything is done automatically.
The Printronix Auto ID ODV-2D printer and scanner talk to each other, enabling the scanner to know the location of every barcode label printed. The printer’s built-in scanner automatically finds and grades every barcode and passes the grading information back to the application in real-time. And if a bad barcode is discovered, the scanner tells the printer to back the bad label up and overstrike it so it is not used, automatically reprinting the label without operator intervention.
The easiest and lowest cost solution to fixing any failing barcodes that could cause downstream issues is to find it at the point of print. Labels are assured to pass the customer’s grading requirements and can be placed on a carton and shipped with confidence.
Using the enterprise-grade Printronix Auto ID T6000e and T8000 barcode inspection printers for automated grading and reprinting of unreadable barcodes offers an efficient and effective method to improve your processes and reduce the risk of fines.
Finding and fixing issues immediately saves time, money, and protects your brand reputation with your downstream customer.
Integrated Barcode Inspection Printers Offer Peace of Mind
Printronix Auto ID barcode inspection printers help you improve barcode label quality with automated processing and deliver peace of mind, knowing that each shipment will be delivered with a high quality, readable label. Using our enterprise-grade PrintNet Enterprise remote printer management software, you can also keep track of shipping label quality and generate reports to support you in an audit or to defend against fines and chargebacks.
For more about integrated barcode inspection printers, contact your local representative or book a free session with our printer experts online.