How RAIN RFID and Connected Cloud Platforms Enable Complete Traceability, Transparency, and Trust
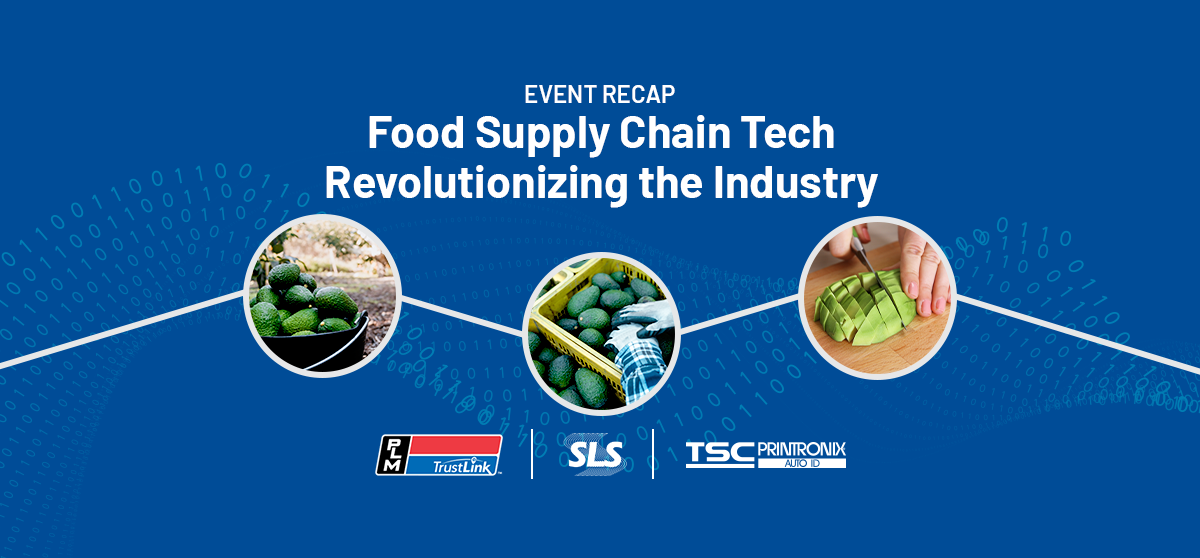
In our recent webinar, co-sponsored by PLM TrustLink and SLS RFID Solutions, we followed avocados from farm to restaurant to detail how TSC Printronix Auto ID products, along with PLM TrustLink and SLS RFID Solutions, made the process run much more smoothly and efficiently with full traceability.
During the presentation, panelists shared their knowledge on certain solutions for the process and answered questions from the audience. With specialized knowledge in IoT technology, RAIN RFID, GS1 encoding standards, and the Food Safety Modernization Act (FSMA) compliance, this conversation covered all the bases for how these products and systems work to streamline each step along the journey to deliver better traceability, transparency, and trust in the food supply chain.
Read more here about how food products are tagged with RAIN RFID labels that are printed and encoded using enterprise-grade thermal printers, then tracked through the supply chain with sophisticated cloud-based software tools as they interact with state-of-the-art readers and portals.
From the Farm: RFID Labels in the Field
The journey begins at the avocado farm in southern California, where food products are assigned their digital IDs. In this scenario, the worker prints and encodes RFID labels in the field using a TSC Printronix Auto ID RFID mobile printer, whose remote technology allows for Bluetooth®, Wi-Fi, and smart battery connectivity to mark the collection bins with such information as fruit type, batch number, harvest location, and date picked. After harvesting, the fruit is carefully sorted depending on customer requirements by item, carton, or pallet levels.
The mobile RFID barcode labels provide a quick and easy approach to print and ensure GS1 standards, on-site and on-demand. Throughout the process, the product information is maintained and digitized in the cloud. Tracking and tracing throughout the supply chain helps to guarantee the products are correctly identified, and when you’re digitizing at the point of harvest, you are ensuring the correct product will be received at the end.
Distribution: Smart Label Solutions
The next leg of the journey is with the wholesale distributor, where the avocados arrive at Drake’s Foods in Worthington, Ohio. As the cartons come off the trucks, smart labels are read by the SLS D-Series Portal and matched against their digital twins in the TrustLink cloud. The cartons are then put away according to the warehouse management location instructions. When a customer order is received, correct items are picked, stacked, and moved to processing.
At the processing station, the operator bags the fruit from farmers, generating a new lot number for the customer case pack. The operator uses a TSC Printronix Auto ID T4000 Enterprise Industrial Printer to print and then encode the RFID labels. This digitizes the new cartons and updates the digital twin with verified cases sent to customers. The freshly packed cases are processed with automated verification using a specialized RFID Tunnel from SLS.
Verified cases are loaded on pallets for specific customer orders. At the pallet wrap station, the digitally marked labels are read by the integrated SLS reader and verified against the customer order. The TrustLink software triggers the T6000e Enterprise Industrial RFID Printer to print the label for the pallet. Now ready for transit, this process ensures that the right products are loaded onto the right truck, for the right customer order.
Restaurant Arrival: RFID Readers and TrustLink Software
On the final part of this journey, the avocados arrive at the restaurant, Drake’s Mexican Grill, where they’ll complete the order. Because of the combined powers of TSC Printronix Auto ID, PLM TrustLink, and SLS RFID Solutions, the organic avocados are received quickly and efficiently. Using an RFID reader and TrustLink software, the product is checked for the correct count, SCU, expiration date, and any holds or withdraws for recalls. The entire journey comes with full traceability, seeing where it came from and what useful information can be gleaned from start to finish.
The result of this process? Complete food traceability, transparency, and trust until it safely reaches the consumer. Though there are many components from the farm to distributor to restaurant journey, the tools and software throughout have aided in saving time, money, and potential compliance issues.
For more information on our food and beverage solutions, explore our webpage or contact your local representative to determine which solution is right for your organization. If you missed the original webinar, you can listen to the webinar at this link.