TSC Printronix Auto ID and Progressive Label Partner to Reduce Chargebacks for This Apparel Supplier with Barcode Verification Printers
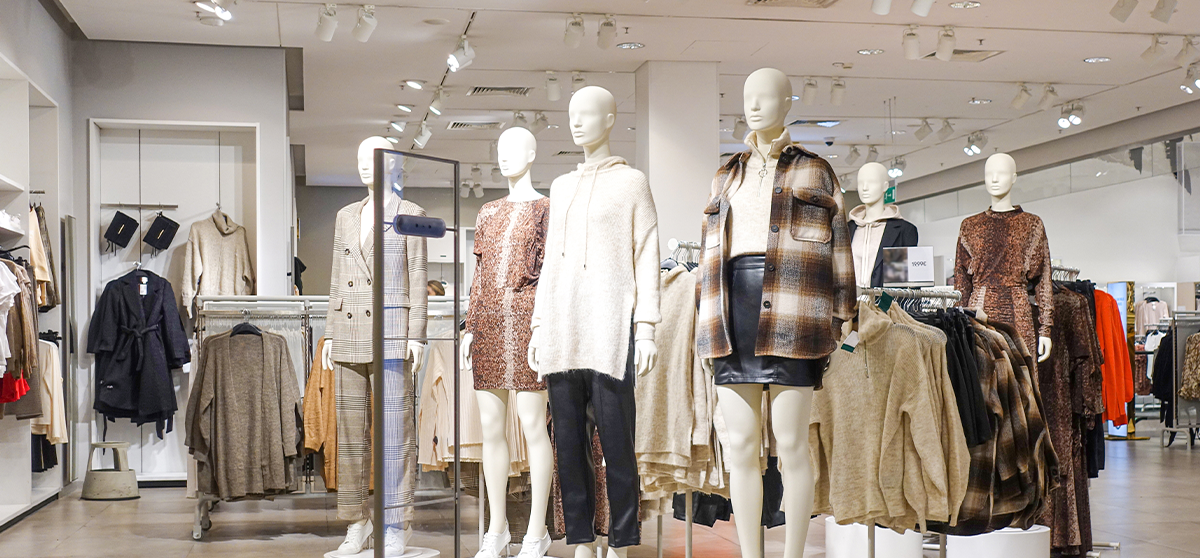
Major retailers receive hundreds of pallets every hour in each of their distribution centers from dozens of manufacturers and suppliers. If an incoming carton’s barcode label can’t be read quickly and easily, retailers will pass this cost along to the suppliers. How can suppliers prove that printed labels were scannable when they left their facility?
Our partner, barcode equipment and label supplier Progressive Label based in Commerce, Calif., worked with an apparel supplier to a major U.S. retailer who was facing this exact scenario: consistent five figure chargebacks from the retailer due to “poor quality labels.” After trying several printers and label types without reducing chargebacks, the supplier was desperate for a solution to improve label quality and reduce the fines.
Keep reading to learn how this apparel supplier deployed TSC Printronix Auto ID barcode label inspection printers and detailed label reports to reduce chargebacks.
Gaining Control Over Unreadable Barcode Labels
Working with Progressive Label, the apparel supplier tried using different labels to enhance quality and accuracy. This included printing at 300 dpi on the highest quality labels — a synthetic polyester label used in the chemical industry with a glossy coat and rated with a 5-year lifetime. These types of labels are also abrasion and scuff resistant, so they are less likely to be damaged in transit to the retailer's distribution warehouses.
The apparel supplier also manually spot-checked the labels before they left their warehouse to ensure the barcodes were readable, but did not have any evidence to back up their manual verification. Despite their efforts, the retailer still claimed the barcodes were bad and imposed fines.
“Having been in the label converter industry for many years, I was confident we were supplying our apparel industry customer the best possible labels. So, when we determined the labels were not the problem, I recommended the customer try the Printronix Auto ID ODV-2D integrated barcode inspection system to fully document their printing process,” said Adam Flores, RFID and Barcode Printing Specialist at Progressive Label.
Taking Charge of Chargebacks with the T8000 Barcode Inspection Printer
After consulting with Progressive Label and receiving a printer demo, the apparel supplier selected five enterprise-grade Printronix Auto ID T8000 enterprise printers with the ODV-2D barcode inspection system. This integrated system has a built-in scanner for space savings while automatically finding and grading every barcode label during the printing process, delivering efficiency. Without requiring operator intervention, the T8000 printer identifies bad labels, retracts them and overstrikes them, reprinting a readable label and passing this information back to the application in real-time.
The Progressive Label team also recommended PrintNet Enterprise (PNE) software, which provides reporting that displays detailed barcode label data. These reports automate the process of recording label quality, reducing manual inspection errors and enabling the supplier to easily access data that proved the barcode labels were compliant before they left their warehouse.
“I encourage my customers to provide a complete print report with their shipment to document to their retail partners that their labels were printed accurately and with high- quality,” added Flores.
Delivering ROI with Automated Barcode Label Inspection and Reporting
Flores added that the TSC Printronix Auto ID barcode inspection solution is available at a very affordable price point. Reducing chargebacks with PNE label reporting also enhances the printers ROI.
The apparel supplier was able to reduce chargebacks by proving that their labels were good quality when they left their facility. The key to reducing their chargebacks was using a printer that could provide a pass/fail barcode grade for every label and generate PNE reports as evidence against proposed chargebacks. By proving their labels were readable, they were able to reduce fines and improve profitability.
To learn more about the T8000 enterprise-grade barcode inspection printer, contact your local representative or schedule a free consult online with one of our experts.