How 2D Barcodes Are More Effective When Label Space Is Limited
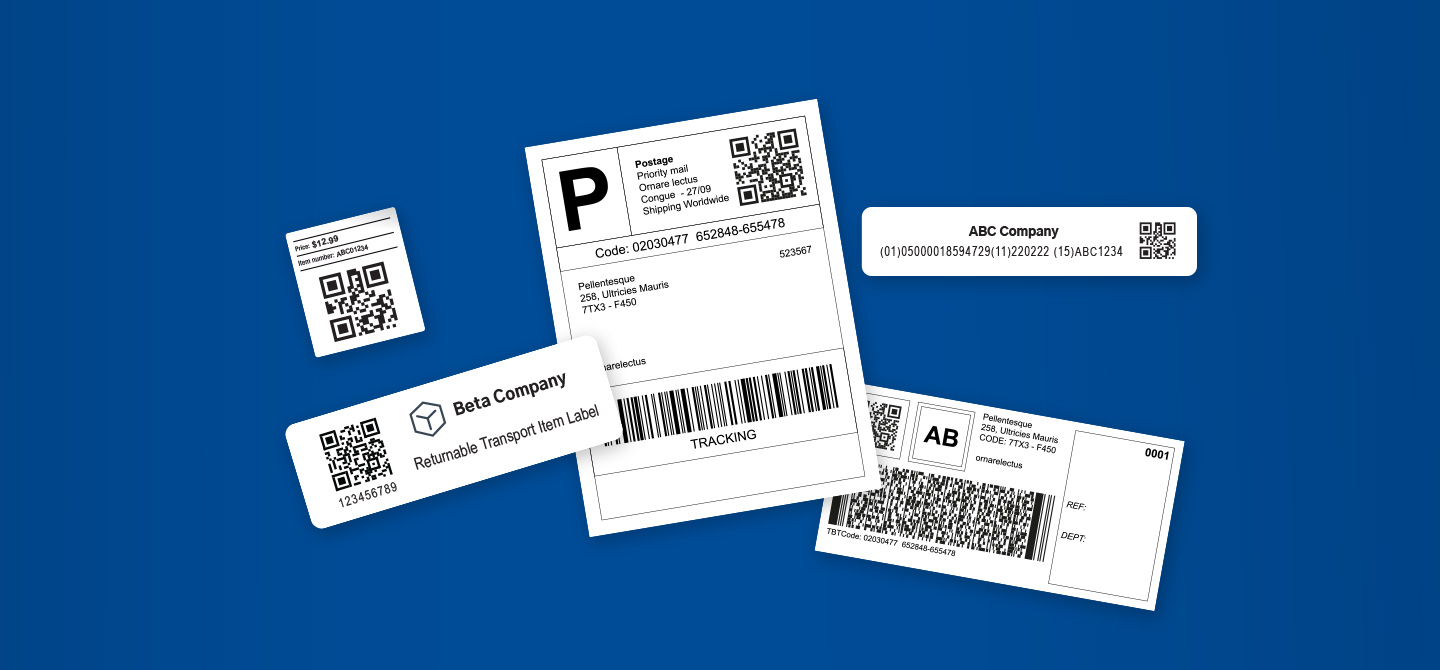
Barcodes are ubiquitous for their ability to transfer tremendous amounts of data rapidly using nothing more than ink on paper. For a low cost, high speed way to transfer thousands of bytes of data, barcodes remain the technology of choice.
Barcodes were originally designed for laser scanners in supermarkets, so they needed to be orientated as a straight line so the scan line could sweep across the barcode (known as 1D barcodes). This meant that as barcodes added more data, the barcode grew in length.
Keep reading to learn more about how designers adapted to increased 1D barcode length and why leveraging 2D barcodes is an effective way to save space on the label and reduce label size, while accommodating growing barcodes.
Adapting to Longer Barcodes and Limitations of 1D Barcodes
At some point barcodes grew so long that they no longer fit in the desired space, confronting designers with a choice of making each bar in the barcode narrower or increasing the width of the label. As there is a lower limit to how narrow each bar can be and still be read robustly and accurately, ultimately some designers were forced to increase label width to accommodate the essential barcode data. Alternatively, designers split the barcode into multiple pieces which required additional scans and processing time at the receiving location.
Wouldn’t it be nice to have a “carriage return” key for a barcode to simplify this? Some 1D barcode symbologies were developed that did exactly that—split the long 1D barcode into multiple sections stacked on top of one another. This was a temporary fix, but demand for more data kept pushing these barcodes to become larger and larger.
The development of optical scanning provided the solution to allow barcodes to be expressed in a more compact form. Rather than sweeping a laser across the barcode, a camera took a picture of the barcode and interpreted software analyzed the barcode. This not only provided freedom for 1D barcodes to be placed in any orientation on the page, but it also enabled the development of 2D barcodes. 2D barcodes could encode information in two directions, enabling a very compact method of packing in data.
For example, look at a typical 4x6 label with identical data and size encoded in 1D and 2D formats:
- The 1D barcode is too large to fix across the width of the 4-inch label and must be rotated.
- The 2D barcode can easily fit in either orientation of the label with plenty of room to spare.
Below is an example of a 2D small barcode (top) and the same exact data in a 1D large barcode (bottom).
Leveraging 2D Barcodes for Data Expansion
As regulatory agencies and receiving customers demand more data on the incoming label, space becomes a premium. The ability to transfer data using a barcode that is 93% smaller (in the example above) opens up significant design flexibility. No longer is the orientation of the label dictated by the barcode. In the above example, over 40 bytes of data is transferred in the space of a single character with a 20-point font size. High efficiency data packing enables significant additional information to be transferred using existing label sizes, or label sizes might be reduced, potentially eliminating the necessity for a wider printer and media.
Labels are an essential element of the supply chain. They enable goods to be delivered and the receiving warehouse to rapidly capture data about the shipment. As more data is requested on the label, the label size is under pressure to expand, increasing cost. Leveraging 2D barcodes is an effective way to save space on the label while reducing label size.
2D Barcodes and Verification Technology
Linear 1D barcode labels can only grow in one direction. Whereas 2D barcodes, or matrix technologies, can grow in two dimensions, enabling more information to be packed into a smaller space.
Our enterprise-grade T8000 and T6000e printers work with 1D and 2D barcodes and feature our integrated barcode inspection system that is tied into the print controller to automatically retract and overstrike bad labels and reprint them. The optical scanner in the ODV-2D verifier reads and grades up to 50 barcodes on a label, assuring better quality and compliance for any barcodes on the label.
While 1D barcodes have been the industry workhorse for a long time, upgrading to 2D barcodes enables you to expand with the demands of our current marketplace. And our barcode inspection printers support automated verification and validation of either 1D or 2D labels, so you can print, verify, and ship with total assurance for quality and compliance.
Learn more about our barcode inspection printers online, or contact your local TSC Printronix Auto ID representative to learn more about 2D labeling.